Newsroom
Reasons for rotary kiln tyre cracks
2021-11-29 | Editor:
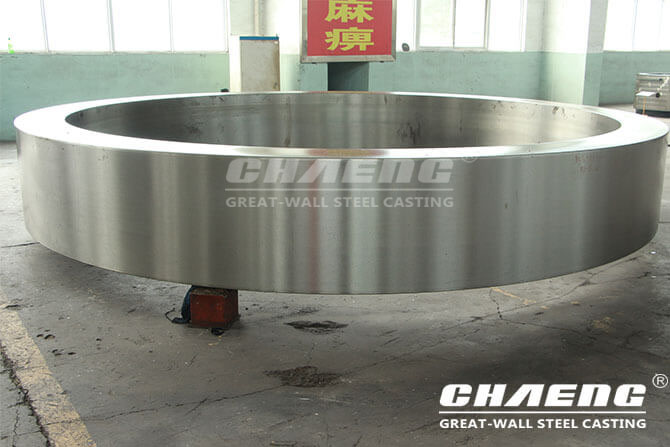
(1) Mesh cracks and large spalling defects occurred on the surface of the tyre, resulting in early abnormal contact fatigue cracking of the tyre.
During the operation of the rotary kiln, the surface of the kiln tyre actually bears a cyclical dynamic load. In the 3-4mm and 5-7mm positions of the tyre skin layer, there are alternating loads and pulsating loads. Under the action of this stress, the microcracks are parallel to the contact stress or form an angle of 45 degrees. With the effect of crack propagation and other external bending distances, the cracks further develop in the skin and depth direction, and even penetrate and brittle, causing the surface to peel and damage.
The main reason for the early contact fatigue cracking of the rotary kiln tyre skin is that after the tyre is put into operation, the wear on the surface of the high hardness segregation zone is less than the wear on the normal area, which causes the surface of this area to bulge and cause stress concentration. Under the action of this stress, where there are non-metallic debris on the surface of the tire and where there are defects such as casting sand holes, microcracks will form first, and external conditions, such as the penetration of corrosive media (cooling water), the kiln Movement, tyre temperature difference, etc., will accelerate the cracking of the tire.
(2) Brittle fracture at low temperature. When the temperature is below 0 degrees, the tire material generally has a very low impact value, and there is almost no plastic deformation ability. Therefore, under low-temperature conditions, small stress is sufficient to cause brittle fracture of the tire.
Rotary kiln tyres are large steel castings, and there are inevitably casting defects such as sand holes, slag inclusions, and inclusions. According to investigations, most of the origin of the cracks on the inside of the tyre are blisters and slag. Under normal circumstances, the kiln is shut down for maintenance, and the temperature of the kiln body is reduced from 150-300℃ to atmospheric temperature. The entire kiln body will be shortened, causing uneven internal stress in the tyre, and changes in the point of action between the tyre and the tug. The sudden start of the cold kiln caused the brittle fracture of the tyre that was in a low-temperature brittle state. Tyre brittle fracture at low temperature occurs mostly in winter and spring.
Order online
Fill out your message and submit it . Options with * must be filled in.
PRODUCTS
CONTACT
- Tel: +8615290747879
- Whatsapp: +8615290747879
- E-mail: casting@chaeng.co
- Skype : GreatWall1958