Newsroom
Sand casting girth gear making process
2019-12-24 | Editor:
CHAENG is specialized in manufacturing steel castings through sand casting process, especially the key product girth gears have been exported to many countries and areas to assist the operation of customers’ ball mill and rotary kiln.
CHAENG adopts adopts the advanced water glass sand molding process, which has higher density and viscosity. And CHAENG has professional technical team to strictly control molding size and molten steel temperature, so as to strengthen hardness and wear resistance.
The making process of CHAENG casting girth gear:
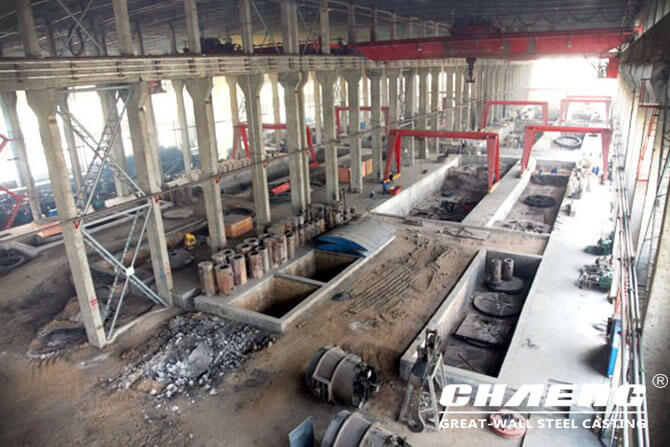
Base on the requirements of customers, CHAENG selects appropriate wooden mold for modeling design, and uses CAE software to simulate the casting process. Strictly according to the process procedures to produce high-quality girth gear:
wood mold - modelling - pouring - heat preservation - out of the pit, sand cleaning - heat treatment - roughing, finishing - packing and delivery.
Advantages of CHAENG casting girth gear:
1. Special Heat Treatment Technology
CHAENG adopts special heat treatment technology to optimize structure, improve hardness and enhance impact resistance of girth gear.
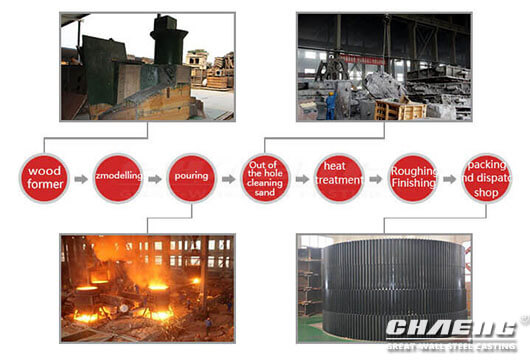
2. Long Service Life
CHAENG adopts high strength steel to produce girth gear. Firstly characteristics optimization of rotary kiln is done to guarantee its stability during long time operation, also to prolong its working life.
3. Factory Price Custom & Quick Delivery
CHAENG has strong steel casting production capability, and it can provide girth gear in large quantity with short period.
Order online
Fill out your message and submit it . Options with * must be filled in.
Prev:Rotary dryer girth gear manufacturer - CHAENG
Next:Problems and measures in the usage of slag pot for iron works
PRODUCTS
CONTACT
- Tel: +8615290747879
- Whatsapp: +8615290747879
- E-mail: casting@chaeng.co
- Skype : GreatWall1958