Newsroom
Head structure of ball mill
2018-06-05 | Editor:
The ball mill head is the general name of the cylinder end cover and the trunnion. It bears the rotation load of the whole mill and the grinding body. It runs continuously under the action of alternating stress. It is also the weakest link of the ball mill, and the most difficult to control the manufacturing quality. The mill head of the ball mill has the following structure form:
Structure form 1: the end cover and the trunnion are cast into one whole. This form is simple in structure and convenient in installation, and is suitable for small and medium size mills. For large diameter mill, it is easy to produce casting defects, because the end cover occupies a large flat area and is relatively thin, even if more risers is used during casting, the cooling shrinkage is not uniform, so that the transition surface of the trunnion and the end cover produces greater stress and looseness. This defect is sometimes found in the cutting process to a certain extent, resulting in undue waste of rework. Sometimes this kind of defect is in a concealed state and can not be found in time, because the part bears the alternating stress and has a large stress concentration during ball mill is running, and the fracture occurs after a period of time, then greater loss will happen.
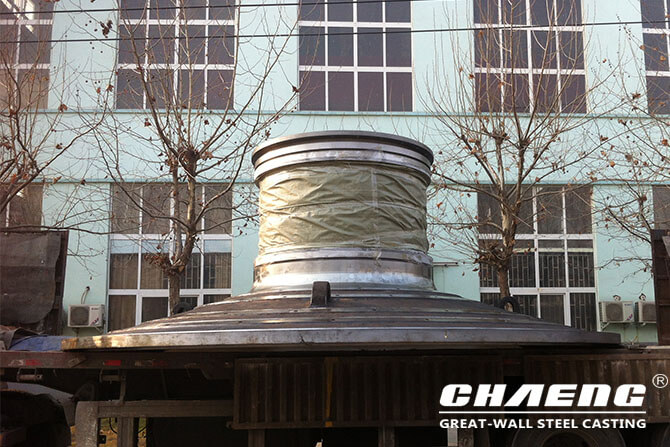
Structure form 2: The end cover and the trunnion are divided into two parts and then combined together. The end cover and the trunnion are respectively cast and assembled together with bolts after processing, end cover uses steel plate welded structure. This structure avoids the above-mentioned casting defects. Although this can solve some problems, but consumes more raw materials and processing workload, and increase the workload of the installation. The advantages of this structure are that the manufacturing process is simple, the cutting process and cutting surface are less, the raw material consumption is less, the end cover quality can be guaranteed, and casting defects do not exist. The end covers are welded to the cylinder body, and the connection is reliable and labor-saving, avoiding the need for bolt or rivet connection.
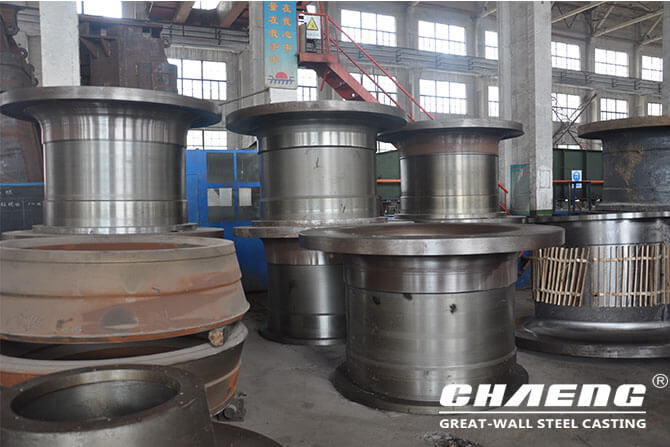
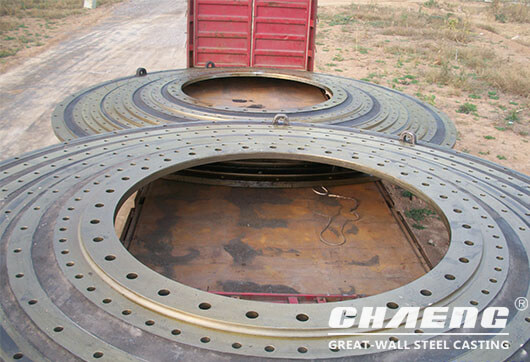
CHAENG, as a professional manufacturer for mill spare parts, can manufacture ball mill head according to customers’ drawings and requirements, using high-quality steel materials and mature technology to guarantee the quality.
Contact us for quotation!
Order online
Fill out your message and submit it . Options with * must be filled in.
Prev:Which is better, the casting girth gear or forging girth gear?
Next:How to solve the poor lubrication of kiln supporting roller bearing in summer
PRODUCTS
CONTACT
- Tel: +8615290747879
- Whatsapp: +8615290747879
- E-mail: casting@chaeng.co
- Skype : GreatWall1958