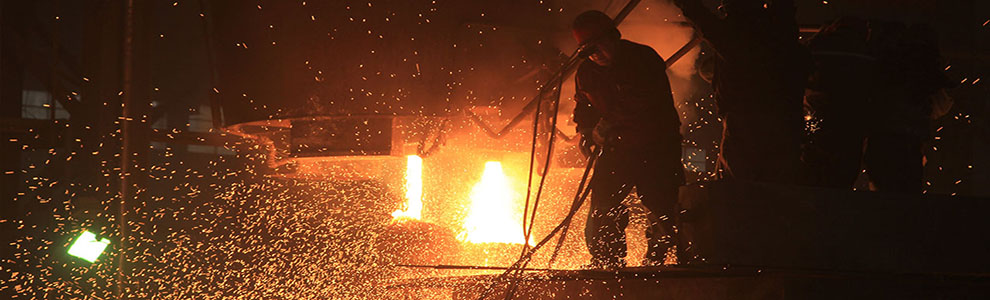
workers tilting a foundry furnace during the casting manufacturing process
What can be found in today’s foundry that creates castings? Similar to a factory’s production line, the manufacturing chain is composed of nine primary sections:
1.First, foundries melt metal to extremely hot temperatures. This requires heating raw metal and/or alloying elements into molten form so it can be poured into molds. In order to achieve these temperatures, specialized furnaces are used. Foundries may house different furnaces based on the type of material or casting process involved.
2.Some metals discharge quantities of hydrogen during cooling. Hydrogen bubbles escape to the top of the surface at the moment of cooling and solidification. This will create porosity on the object’s surface and lead to mechanical and chemical deterioration of the object over time. To combat this, a foundry will employ various types of "degassing" equipment to measure and regulate the amount of hydrogen present in the object.
3.In order to create a casting from an original design, foundries require mold and pattern making equipment. Depending on the casting process involved, a foundry may offer several types of mold making systems. For example, sand casting requires specialized resin bonded sand molds. Investment casting requires the creation of wax patterns and ceramic molds. Die casting involves machining metals into molds using various alloys containing zinc, copper, lead, pewter, and more.
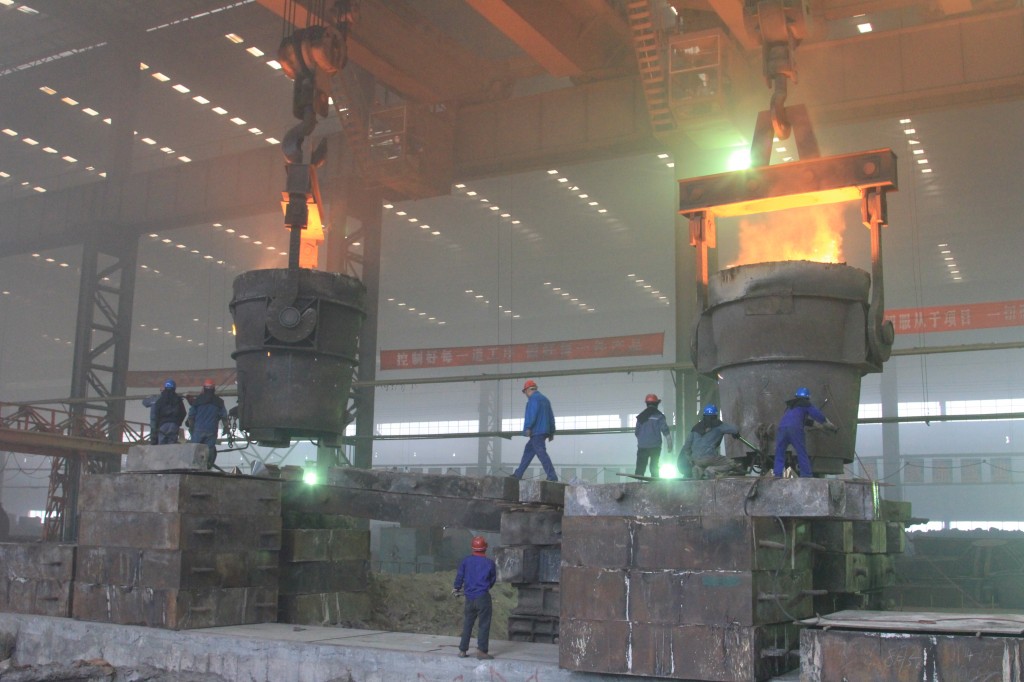
5.Once a mold solidifies, equipment is used to eject the final object from the mold. This requires the use of specialized cutting torches, saw blades, sledge hammers, or even knockout machinery to eject the casting from the mold.
6.Foundries also employ equipment used to heat treat metals in order to alter their physical properties. Using specific techniques in heating and cooling, a metal’s properties are manipulated through annealing, case hardening, tempering, and quenching.
7.Once the casting is ready, its surface properties still require treatment. Excess mold media such as sand or metal particulate need to be removed. In this case, various surface treatments are used. This can include high powered compressed air or surface blasting with beads, metals, or other media.
8.Now that the casting is clean, final finishing takes place. The finishing process involves equipment for grinding, sanding, machining, painting, and welding to achieve whatever is requested by the customer.
Foundries are simply factories that provide steel casting services. Castings are the end product created by foundries. The tools, techniques, and processes used to make castings were berthed under the roof of the foundry. To this day, the pillars of our industry depend on foundries to create castings of all sizes and for every sector of our society.
Prev:4m Large Ball Mill Ring Gear Process Design
Next:Great Wall Steel Casting Manufacturing Process Measures
- Tel: +8615290747879
- Whatsapp: +8615290747879
- E-mail: casting@chaeng.co
- Skype : GreatWall1958