Newsroom
Cement rotary kiln maintenance and overhaul
2018-06-02 | Editor:
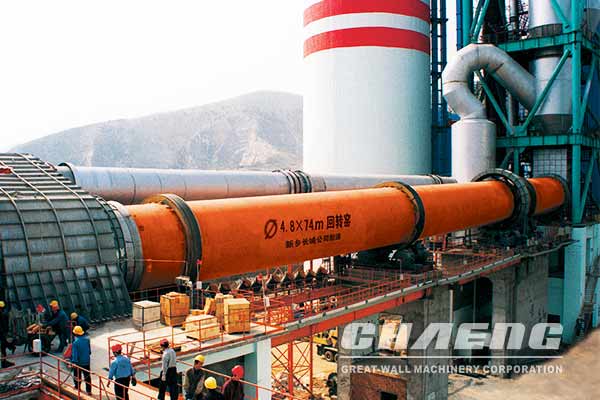
1. All parts of the thrust roller and drive system must be checked once every hour. Abnormal situations such as abnormal sound, vibration and overheating should be dealt with promptly.
2.Check whether the contact and wear between the kiln tyre and the supporting roller are uniform, whether there is excessive stress or surface damage.
3. According to the relative displacement between the kiln tyre and its backing plate in a turn, the clearance and the wear condition are identified, and check whether the backing plate welding positions have cracks. Frequently inject grease into the friction surfaces between the kiln tyre with the backing plate and the stopper.
4. Every shift should check the anchor bolts and fixing bolts of the transmission base and supporting device. If there is looseness, tighten it immediately.
5. Observe the foundation for vibration and sinking.
6. Observe whether the sealing of the kiln tail and head is good and whether the wear is serious.
7. Check the temperature of the support roller shaft and its lubrication condition every hour, and observe whether the clearance between the thrust ring and the lining is in the normal state.
8. Periodically check the auxiliary drive system. Drive the auxiliary drive system without connecting the clutch once every week, in order to ensure the smooth start when the main power supply is suddenly interrupted.
9. Regularly inspect the temperature of the cylinder, especially the temperature of the burning zone and the intermediate zone near the thrust roller and other attachments, the temperature should be maintained below 380 °C. Only occasionally, it is allowed to reach 410 °C. If it exceeds 415°C and continues to operate without processing, it is unprofessional operation.
The overhaul of rotary kiln
During the operation of rotary kiln, the wear of parts and the reduction of equipment accuracy will affect the running rate of rotary kiln. Repair and replacement work must be carried out. Under the principle of preventive maintenance, maintenance plans should be prepared in advance. At present, the main repair methods are minor repairs and medium repairs. They are usually performed when rotary kiln is stopped to install the lining. Larger medium-repairs are preferably carried out in phases at 2 and 3 times of kiln lining installation. The overhaul of drive system should be carried out after the installation of lining, and should be completed as soon as possible (eg 8-12 hours). The capital repair spend long overhaul time (for example, 10 to 20 days), during which all the worn parts should be replaced, all units should be checked and adjusted (such as the replacement of the cylinder section, ring gear, tyre, support roller, thrust roller and other important parts; alignment of the kiln center line, etc.)
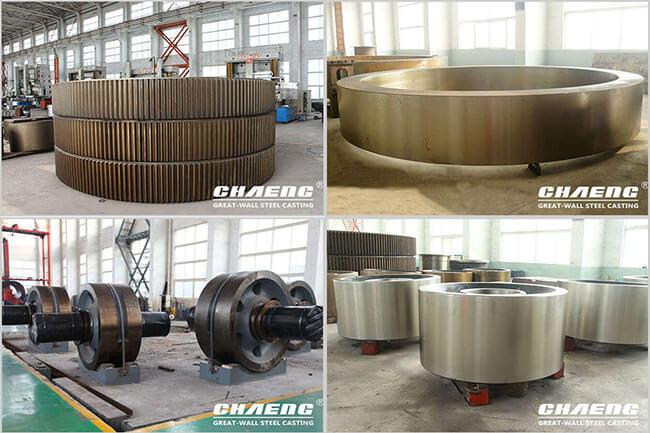
The repair and replacement standards for the main wear parts of the rotary kiln are as follows:
1. The tooth thickness of the drive gear wears 30%, or the rim has irrecoverable damage;
2. There are cracks or local deformations in segments of the kiln shell;
3. The wear of the kiln tyre section is 20%; or the surface is worn into conical or polygonal, and localized through-hole cracks appear;
4. The journal diameter of the supporting roller and the thrust roller is reduced by 20%, or the thickness of the support roller rim is worn out by 25%; the rim is worn into conical or other specialties, or the rims have cracks through them. When changing the supporting roller and the thrust roller, the corresponding liners must be re-ground or replaced.
CHAENG (Great Wall Steel Casting) is professional manufacturer supplying support roller, tyre (riding ring), girth gear, kiln segments, thrust roller for rotary kiln according to users’ drawings and requirements, guaranteeing good adaptability to your kiln and reliable quality certificated by ISO 9001:2015. Contact us!
Order online
Fill out your message and submit it . Options with * must be filled in.
Prev:CHAENG slag ladle types for foundry
Next:Which is better, the casting girth gear or forging girth gear?
PRODUCTS
CONTACT
- Tel: +8615290747879
- Whatsapp: +8615290747879
- E-mail: casting@chaeng.co
- Skype : GreatWall1958