Newsroom
How to prolong the life of vertical roller mill grinding roller
2016-07-16 | Editor:
Industrial vertical roller mill in the use of process, should be fixed personnel responsible for the custody, operating personnel must possess a certain level of technology. Mill before installing the operating personnel must carry out technical training necessary to understand the principle,performance of the pulverizer, familiar with the operating procedures.
In order to make the milling machine is normal, should make the "equipment maintenance equipment safety operation system" to ensure the long-term safe operation maintenance tool grinder, while necessary and grease and the corresponding accessories.
Milling machine is used for a period of time, should be carried out maintenance, and repair replacement treatment on roller grinding ring bladewearing parts, grinding roller device, a careful examination of the connectingbolt and nut should be in use before and after, to see whether there is loose,grease is full.
More than 500 hours to replace the roller using time grinding roller device, therolling bearing of roller sleeve must be cleaned, the damaged parts should be replaced, fueling tool available manual oil pump and a grease gun. Fineness regulation, according to the different material size, hardness, moisture content,specific gravity, processing thickness is different, can be adjusted at the top of the analyzer, high speed, high fineness, low speed, low fineness. Improve thefineness, the yield will be reduced accordingly, if not up to the requirements shall be debugging fan speed, the user can flexibly mastering. Wear limit scrapring roller, the remaining minimum wall thickness shall not be less than 10mm.
Stop, stop feeding, host still continue to live, so that the residual abrasivecontinue grinding, after about a minute, can close the electric motor and the parser motor, stop grinding work, then stop the fan motor, in order to purgeresidual powder.
In order to make the milling machine is normal, should make the "equipment maintenance equipment safety operation system" to ensure the long-term safe operation maintenance tool grinder, while necessary and grease and the corresponding accessories.
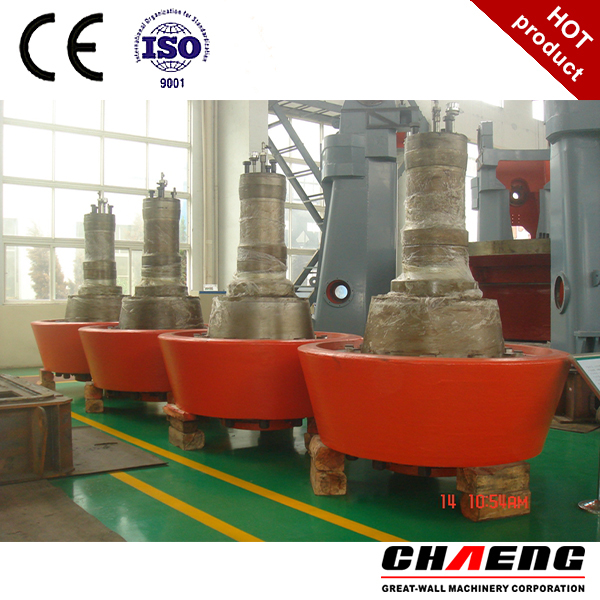
More than 500 hours to replace the roller using time grinding roller device, therolling bearing of roller sleeve must be cleaned, the damaged parts should be replaced, fueling tool available manual oil pump and a grease gun. Fineness regulation, according to the different material size, hardness, moisture content,specific gravity, processing thickness is different, can be adjusted at the top of the analyzer, high speed, high fineness, low speed, low fineness. Improve thefineness, the yield will be reduced accordingly, if not up to the requirements shall be debugging fan speed, the user can flexibly mastering. Wear limit scrapring roller, the remaining minimum wall thickness shall not be less than 10mm.
Stop, stop feeding, host still continue to live, so that the residual abrasivecontinue grinding, after about a minute, can close the electric motor and the parser motor, stop grinding work, then stop the fan motor, in order to purgeresidual powder.
Order online
Fill out your message and submit it . Options with * must be filled in.
Prev:Great Wall Steel Casting big modulus girth gear
Next:Slag pot manufacturer take the route of middle and high-end
PRODUCTS
CONTACT
- Tel: +8615290747879
- Whatsapp: +8615290747879
- E-mail: casting@chaeng.co
- Skype : GreatWall1958